Gas Manifold System
We provide the installation of Manual & Automatic compressed gas manifolds for the Commercial, Industrial & Medical sectors. Our gas manifolds are fitted to the industry standard.
Manual Manifold Features
2 x Isolation valves
Single or Multi-stage regulator
Isolation valves
Purge valves
Safety relief valve
Flexible cylinder hoses
(Pigtail or flexible hose and heatsink for Oxygen)
High and low pressure gauges
High pressure non-return valves
Line valve and union
Flashback arrestor for flammable gasses
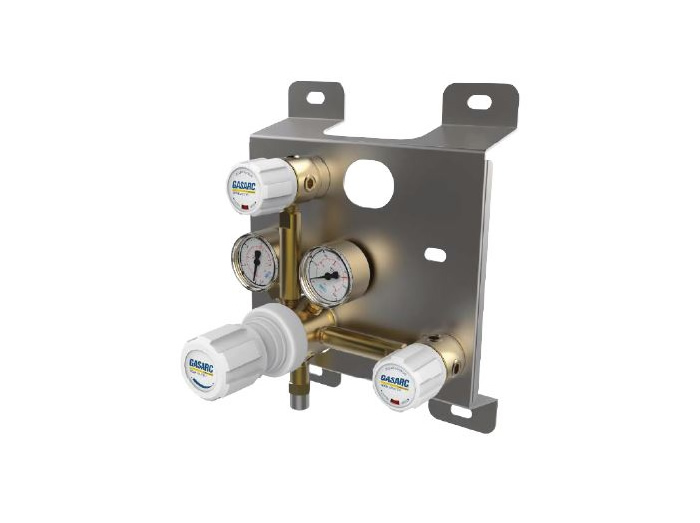
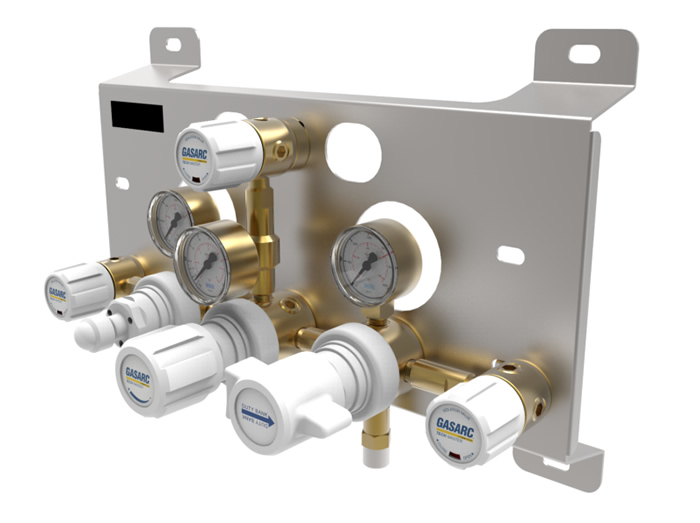
Automatic Manifold Features
Up to 300 bar inlet pressure
To supply non-corrosive gases from single or multiple sources.
For primary pressure control for gases up to Grade 4.5 (99.995%)
Cylinder or MCP (multi-cylinder pack) supply
What are compressed gas manifolds?
A gas manifold system is used to distribute compressed gases from a centralized source to various points of use. These manifolds typically consist of a series of interconnected valves, pipes, and fittings that allow multiple compressed gas cylinders or other high-pressure sources to be connected and regulated together.
The purpose of using a compressed gas manifold system is to provide a reliable, continuous supply of high-pressure gases to various locations within a facility. This can be especially important in industries such as manufacturing, healthcare, and research, where compressed gases such as oxygen, nitrogen, and helium are used for a wide range of applications.
Manifolds can be customized to meet the specific needs of a particular facility, including the number and type of gas sources, the number of outlets, and the flow rates and pressures required. They can also include safety features such as pressure relief valves, check valves, and alarm systems to ensure safe and efficient operation.
What is needed to achieve a gas manifold system install?
Fitting a gas manifold system involves a series of steps to ensure that the manifold is installed safely and correctly. Here are the general steps to follow:
Choose the correct manifold: Make sure that you have selected the correct manifold for your application. This includes verifying that the manifold is designed to handle the specific type of gas and pressure that you will be using.
Prepare the workspace: Before installing the manifold, make sure that the workspace is clean and free of debris. This will help to prevent contamination of the gas lines.
Shut off the gas supply: Turn off the gas supply to the area where the manifold will be installed. This can usually be done by turning off the main gas valve.
Install the manifold: Connect the gas manifold to the gas lines using appropriate fittings and connections. Follow the manufacturer's instructions carefully and ensure that all connections are tightened securely.
Test for leaks: Once the manifold is installed, test it for leaks using a gas leak detector or soapy water solution. Apply the solution to all fittings and connections, and check for bubbles or other signs of leaks.
Turn on the gas supply: Once you have verified that the manifold is leak-free, turn on the gas supply to the area where the manifold is installed.
Test the system: Test the gas system to ensure that the manifold is functioning properly. This can include verifying gas flow rates, pressure levels, and other performance metrics.
Label and document: Finally, make sure to label the manifold and document the installation process. This will help to ensure that the system can be maintained and serviced properly in the future.