Laser Cutting Gas Installation
We use laser cut pipework for the installation of single-cylinder manifolds or multi-stage regulators.
This precision method is required when providing cuts for joints for the following typical high-purity gases
Helium
Nitrogen
Carbon Dioxide
The latest Fiber laser machines only require high-pressure gases for the cutting process.
Gascare Services offer a complete solution to your gas installation, from the manifold to the outlet position making sure all pipework is cut using the laser
Upon completion of installation and successful strength and leak testing a certificate is issued.
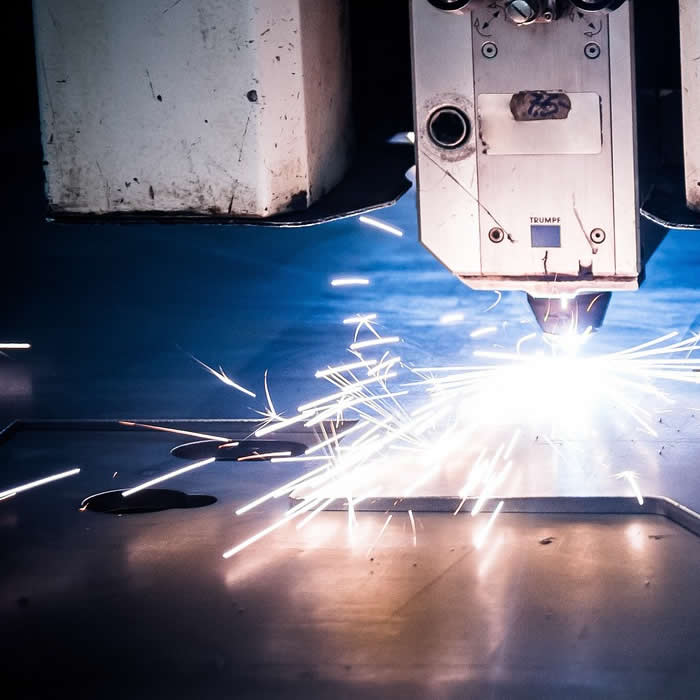
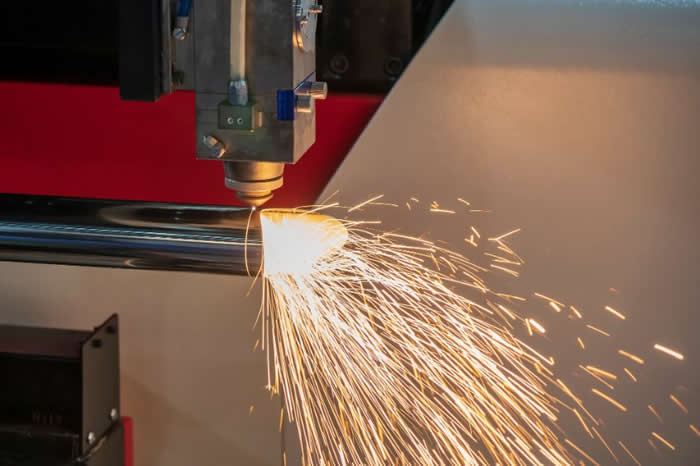
Certified Laser Cut Pipework
Gascare Services offer a complete solution to your laser cut pipework gas installation, from the manifold to the outlet position.
Our competent engineers will install your piped gas installation to the requirements of the BCGA (British Compressed Gas Association) Codes of Practice.
The majority of laser cutting machines require either Nitrogen or Oxygen gas (even both) delivered at high pressure.
The gas is supplied via cylinders (MCP) or bulk tank and will need a gas system capable of withstanding up to 31 bar.
The laser gases are supplied via single cylinders, and it is critical that the gas supply is Grade 5 (99.999%) high purity to prevent impurities affecting the laser process.
Why use a laser to cut the pipework?
Precision: Laser cutting offers high precision, allowing for clean and accurate cuts, which is especially important in pipework where precise measurements and tight tolerances are required for proper fit and function. Laser cutting can produce complex shapes and intricate designs with minimal distortion or heat-affected zones.
Speed: Laser cutting is a fast process, with the ability to cut through various types of pipework materials quickly and efficiently. This can lead to increased productivity and reduced production time, making it a cost-effective option for large-scale pipework cutting projects.
Versatility: Laser cutting is highly versatile and can be used for cutting a wide range of materials commonly used in pipework, such as stainless steel, carbon steel, aluminium, and copper, among others. This makes it suitable for cutting pipes of different shapes, sizes, and thicknesses, allowing for greater flexibility in pipework fabrication.
Clean and Burr-Free Cuts: Laser cutting produces clean and burr-free cuts, minimizing the need for additional deburring or finishing processes, which can save time and labour costs. The absence of burrs also reduces the risk of contamination in pipework systems, ensuring smooth flow and preventing potential issues.
Non-Contact Cutting: Laser cutting is a non-contact process, which means there is no physical contact between the cutting tool and the pipework material. This eliminates the risk of material distortion, warping, or damage due to tool wear, resulting in precise and consistent cuts.
Automation: Laser cutting can be easily integrated into automated systems, allowing for high-speed and high-volume pipework cutting with minimal human intervention. This can result in increased production efficiency, reduced labour costs, and improved safety by minimizing human interaction with hazardous pipework materials.
Minimal Waste: Laser cutting produces minimal waste compared to traditional cutting methods, as the laser beam is highly focused and generates narrow kerfs, resulting in optimized material utilization. This can lead to cost savings in material costs and disposal fees.
Customization: Laser cutting allows for easy customization of pipework components, such as holes, notches, and complex shapes, to meet specific project requirements. This flexibility in design and customization can result in improved functionality and performance of the pipework system.
Safety: Laser cutting can be a safer option compared to traditional cutting methods, as it eliminates the need for sharp cutting tools or blades. Additionally, modern laser cutting systems often incorporate safety features such as enclosed cutting areas, fume extraction, and laser beam guards to ensure operator safety.
Environmental Friendly: Laser cut plumbing is generally considered to be an environmentally friendly cutting method as it does not produce harmful fumes, dust, or noise pollution, reducing the impact on the environment and creating a safer working environment for operators.
Overall, laser cutting offers numerous advantages for cutting pipework, including high precision, speed, versatility, clean cuts, automation capabilities, minimal waste, customization options, safety, and environmental friendliness. It can be a valuable tool in pipework fabrication, resulting in improved productivity, cost savings, and high-quality results.